· Hersh Kshetry · Case Studies · 2 min read
Textile CETP Modernization – 100 MLD Common Effluent Treatment Plant Upgrade
Consulting project to modernize a 100 MLD common effluent treatment plant serving a textile manufacturing cluster with 124 member factories, expanding capacity to 130 MLD
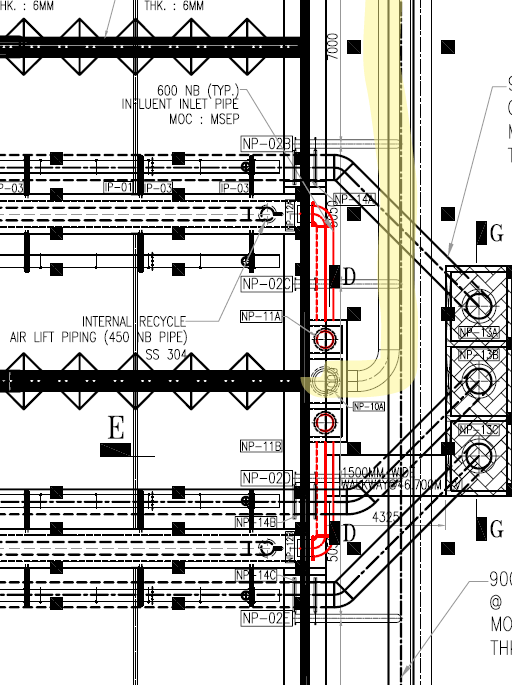
Overview
Consulting project to modernize a 100 MLD common effluent treatment plant (CETP) serving a textile manufacturing cluster with 124 member factories. The CETP, originally built for 100 MLD, needed capacity expansion to 130 MLD and process upgrades to meet stricter environmental norms and accommodate increased production volumes. A detailed technical assessment and upgrade roadmap were developed, allowing the industrial consortium to seek government funding for implementation. The plan emphasized enhancing treatment performance (particularly for high color, COD, and TDS typical of textile effluent) while minimizing new construction by improving the efficiency of existing systems.
Technical Insights
The project team recommended advanced biological treatment improvements and smarter aeration techniques to boost capacity and effluent quality. One key proposal was to retrofit the aeration tanks with integrated clarifier modules that allow much higher biomass concentration and eliminate the bottleneck of traditional settling tanks. This innovation increases treatment throughput within the same tank volume by using inclined plate settlers and airlift sludge return built into the aeration tanks.
Enhanced automation and monitoring (including online sensors for COD, color, flow balancing) were planned to improve operational control across the four parallel treatment trains. The modernization would enable the CETP to consistently meet discharge standards despite higher loads, and even explore water reuse opportunities (e.g. supplying treated water for cooling towers in nearby industries) using add-on filtration and RO units.
Project Team’s Role
The project team identified critical pain points (such as overloaded clarifiers and insufficient aeration in peak dyeing seasons). The team formulated the process upgrade strategy, selecting appropriate technologies to handle the complex mixed wastewater and prepared a Detailed Project Report (DPR) outlining technical designs, phased implementation plans, and cost-benefit analysis.
The team also developed the procurement plan (RFQs for new equipment like screens, diffusers, cooling towers, etc.) and an execution timeline that would allow the CETP to remain operational during upgrades. This technical advisory project provided a clear path to extend the CETP’s capacity by 30% and significantly improve its treatment outcomes, ensuring the textile cluster’s expansion is sustainable and compliant.